Deep mixing pile
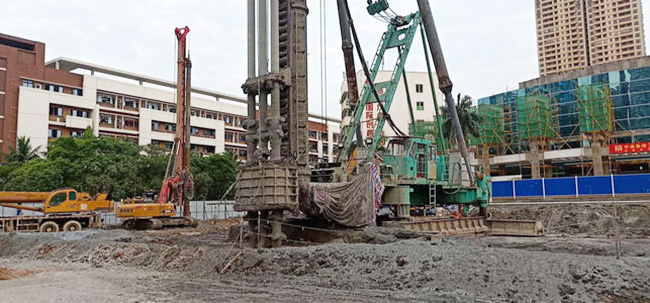
Deep cement mixing pile uses cement as a curing agent, and through deep mixing machinery, soft soil or sand is forcibly mixed with the curing agent on the foundation, making the soft foundation hard and improving the strength of the foundation.
Deep cement mixing piles are suitable for soft foundation treatment and have significant effects. After treatment, they can form piles, walls, etc. Deep cement mixing piles are suitable for handling silt, sandy soil, muddy soil, peat soil, and silt. When used to treat peat soil or groundwater with erosivity, its applicability should be determined through testing. During winter construction, attention should be paid to the impact of low temperature on the treatment effect.
Construction Technology of Deep Mixing Pile
Set out the inner and outer edges of the mixing pile according to the construction drawings. The axis measured during construction should be properly protected after review, and the error between the pile layout and the design drawing should not exceed 5cm. Before the construction of each pile, the verticality of the mixing shaft in two different directions must be corrected. The verticality error should not exceed 5cm.
Measure the elevation of the mixing pile and mark it around the support area to ensure the depth of the mixing pile into the soil.
Dig a sample slot according to the inner and outer edges of the mixing pile. The excavation depth of the sample slot is about 1.50m below the natural ground level.
Promptly remove any obstacles found.
Construction process flowchart
Drilling positioning - preparation of cement slurry - pre mixing and cutting of soil for settling - slurry feeding - mixing and lifting - repeated mixing and sinking - slurry feeding - repeated mixing and lifting - displacement - cleaning
The pre mixed sinking machine is hung on a crane with a steel wire rope, and the storage mortar pump is connected to the deep mixer with a slurry hose. After the cooling water circulation of the deep mixer is normal, it is necessary to wait. Start the mixer motor, loosen the crane steel wire rope, and allow the mixer to sink along the guide frame by mixing and cutting soil under the weight of the equipment. The sinking speed can be controlled by the current monitoring meter of the motor, usually 0.38-0.75m/min. The working current should not exceed 70A. If the sinking speed is too slow, clean water can be supplied from the slurry conveying system to facilitate drilling.
Preparation of cement slurry
It is recommended to use 425 # ordinary Portland cement as the mixing liquid. When the deep mixer sinks to a certain depth, the water slurry should be mixed according to the designed mix ratio. Before grouting, the cement slurry should be poured into the aggregate hopper.
Spray mixing and lifting
After the deep mixer sinks to the designed depth, start the mortar pump to continuously press the cement slurry from the center pipe of the mixer into the foundation, spray the slurry while stirring, and lift it up for about 1-2 minutes until the ground is lifted to complete a mixing process. At the same time, strictly follow the designed lifting speed to lift the deep mixer, usually at a uniform speed of O.5m/min.
Repeat stirring up and down
When the deep mixer is lifted to the top elevation of the designed reinforcement depth, the cement slurry in the aggregate hopper should be completely emptied. To evenly mix the soft soil and mud, the mixer can be rotated and sunk into the soil again. After reaching the designed reinforcement depth, the mixer can be lifted out of the ground to complete a column shaped solid addition, with a shape of "8", and one by one overlapping, forming a wall shaped solid addition. Several wall shaped solids are connected to form a block.
clean
Inject an appropriate amount of clean water into the aggregate hopper, start the mortar pump, and clean all remaining cement slurry in the pipeline until it is basically clean. And clean the soft soil adhering to the mixing head.
If the shutdown is caused by low voltage, blockage of the slurry conveying pipe, or other reasons, the mixing head should be lowered by at least 0.5m after the mixer is restarted, and the spraying pressure should be lower than 0.3MPa before continuing.
The sinking speed of the second mixing should not exceed 2.0m/min, and the lifting speed should not exceed 0.8m/min.
When repeatedly mixing up and down, it is required to spray the slurry evenly along the length of the pile, and the slurry should also be applied after the pile is completed.
The pile length should not be lower than the design value. The pile bottom should be 10-20cm deep, and the pile top should be about 10cm high.
During pile construction, if abnormal vibrations, tilting, or displacement are found in the deep mixer, it should be immediately stopped for inspection, and if necessary, the drill should be lifted and re driven.